CFO Color Sensor
Precise optical inspection at high speed
The CFO color sensors, distributed exclusively by Micro Epsilon, enable optical inspection and validation for your application with highest reliability and precision. Through modeling the signal processing from human color perception there are nearly no boundaries for your detection tasks. Highest precision and sample rates up to 30kHz ensure frictionless online process control without bottlenecks.
Integrate CFO color sensors in today's facilities and you are ready for tomorrow's requirements - classic interfaces and ethernet-based network capability combined with modern web services pave the way towards Industry 4.0.
Get in contact
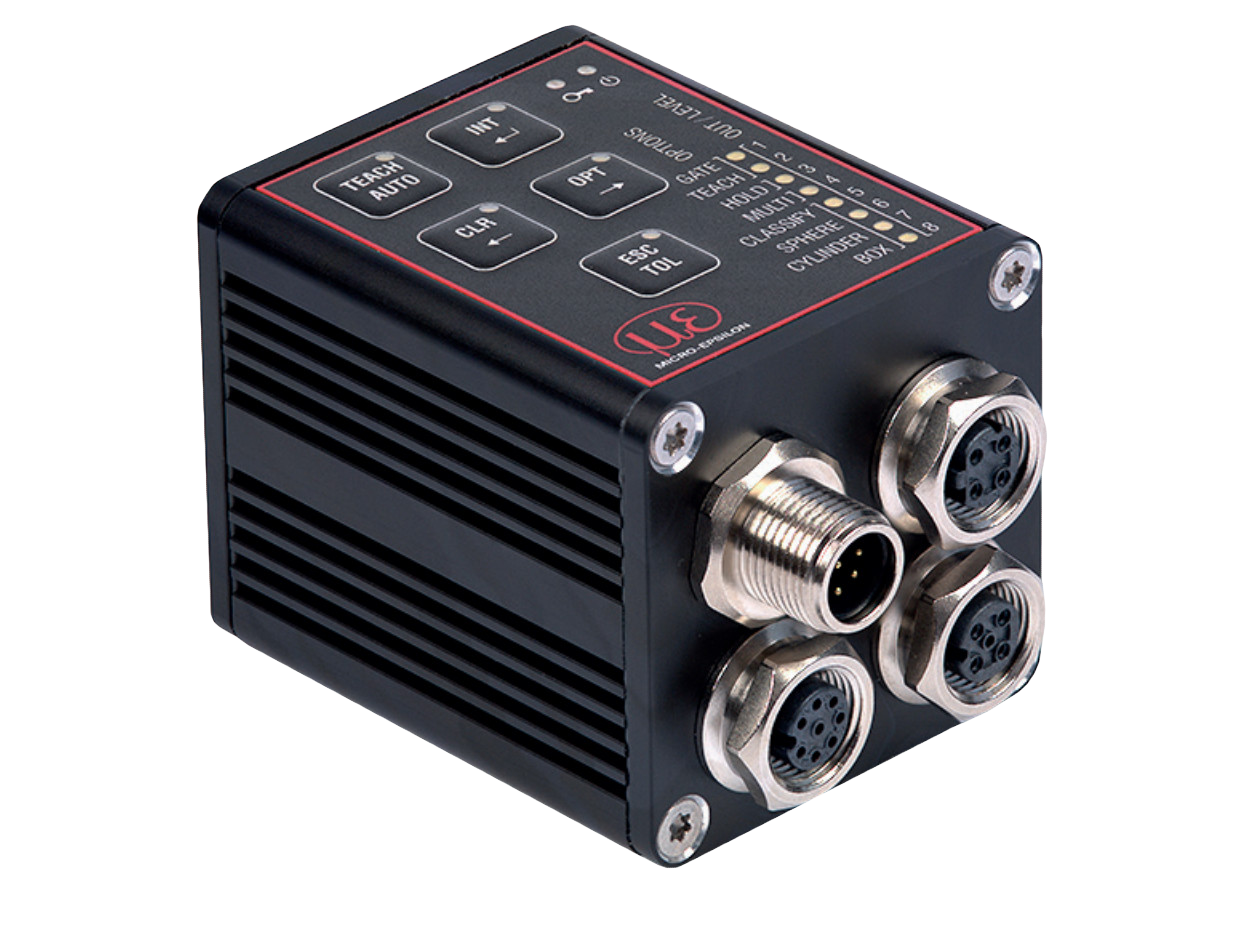
IP-Networkable
CFO supports ethernet-based networks using IP-based protocols - the building blocks of the internet. This way the color sensors can be seamlessly integrated into exisiting company networks.
Everything your IT security department whishes for can be implemented based on tools and applications they already know and value. IP-based networks are proven, established and wildly supported by a all platforms and operating systems.
Sampling rate
CFO color sensors archieve sampling rates of up to 30 kHz. This means every thirty thousandths of a second CFO color sensors can compute a processing step and transmit the results at the switching outputs. If your application has lower performance demands, this extremely high sampling rate allows further optimization of the signal quality through oversampling.
Our hardware never sleeps.
Operation and API
CFO uses newest web technologies to deliver an appealing and functional configuration interface. Our aspiration doesn't halt at creating quality hardware. We also strive for great user interface design and accessibility. And when we say web we mean it: We avoid Java, Flash and other proprietary software solutions as these could potentially endanger your IT infrastructure.
Beyond that our REST API will enable your developers to create reporting and automatization solutions custom-tailored to your production environment. Ask the IP department supporting your production lines: they won't want to miss CFO color sensors.
Feature | CFO100 | CFO200 |
---|---|---|
Reproducability | ≤ 0.5 ΔE | ≤ 0.3 ΔE |
Sampling rate | 10 kHz | 30 kHz |
Switching outputs | 3 | 8 |
High power LEDs | 1 | 1 |
Color spaces | XYZ, xyY, L*a*b*, L*u*v*, u'v'L | XYZ, xyY, L*a*b*, L*u*v*, u'v'L |
Interfaces | RS232, Ethernet | RS232, Ethernet, USB |
Working temperature | -10°C to +55°C | -10°C to +55°C |
Type of protection | IP65 | IP65 |
Datasheet | Datasheet - EN | Datasheet - EN |
PCS Technology
Color perception of the sensor is modeled after human perception, but can differentiate significantly more precisely than the human eye. This enables reliable detection of subtlest color nuances.
Reliable measurements
Averages over many 1,000 of measured values can be computed inside big color spaces - at full sampling rate.
ΔE ≤ 0.3
The finest detectable color distance between two colors equals delta E < 0.3.
Beyond that
Super-bright white color LED
Strong extraneous light compensation
Tolerance spaces per color.
Color sensor CFO in action
Filling and detection of detergent bottles
Bottling applications are among the sensorily demanding use cases. Production is running around the clock in three shifts. Interruptions usually only occour for cleaning or maintenance purposes. An according amount of bottles passes the filling process daily. In detergent filling a filling machine has to ensure that different colored detergents with slight color variations is filled into 1.5l plastics bottles. These machines usually use barrels with carrying capacity in the hundrets of liters. From those barrels the detergent flows into the bottles, controlled bei filling valves. One complete filling machine ususally employs over 100 filling valves each filling up about 300 bottles per minute, resulting in a daily run of about 432,000 bottles.
Additional demands are set by differences of the semi-translucent plastics bottles regarding chromaticity, material thickness, surface properties and form. And for marketing reasons the detergent has slight color varations (lighter pink, darker pink, light and opaque red, dark and opaque red etc.)
Such a filling machine has to ensure that there are no visible deviations regarding consistency, translucency and color within the same batch. If e.g. color or translucency of a detergent changes systematically within the same filling process, this has to be detected immediately. Ideally the plant operator has to be alarmed before the deviation passes the quality tolerance threshold. Additionally the system has to control whether the given detergent variant gets filled into the correct bottle type. Finally the inspection of the correct charge has to be taken care of. Batch changes should be an easy process without any need for reconfiguration of the sensor settings.
The resulting demands besides high working speed are:
- Detection of subtlest color differences
- high reproducability of the detection task
- decision thresholds aligned with human color perception
- high resistance against moist and abrasive environments
- ability to switch multiple valves directly from a single sensor
The CFO200 color sensor, having a sampling rate of 30kHz, color precision of delta E < 0.3, 8 switching outputs and IP65 level of environmental protection, seems to be meant for exactly this type of application. The color sensor allows for easy batch changes by giving the plant operator the option to simply switch between predefined configurations using just a tablet or smartphone. This ensures minimal downtime and eases process security through optional integration of sensor preconfigurations into the process control system.
Tasks
- Monitoring of optical product quality
- Recording of optical product quality indicators
- Assignment of product to product carrier
- Sorting of the end product
- quantity control
Implementation
Two CFO color sensors are designated for every filling machine. One of the sensors combined with optical fiber and optics gets directed at a significant part of the product label on a detergent bottle. The second sensor targets the transparent bottle surface to inspect the optical impression of the filled-in detergent liquid.
The first color sensor has been trained with the different colors of different product labels. Using its eight switching outputs it can give out a unique signal of the bottle type that currently gets filled.
The second sensor has been trained with the different color impressions of the detergent liquids as they appear through the bottle material. For customers this color impression is important for the buying decision. As implemented with the first sensor, the different detected color impressions are signaled through the eight switching outputs.
In-line process control continuously compares the different detection results of both sensors and can decide whether detergent and bottle fit together. Incorrect states are instantly reported to the plant operator.
The accompanying process control records current color impressions of the detergent liquid perodically. This data can later be used for optimizing process parameters. Polling of sensor data is implemented using the REST API of the color sensors. Other information like quantity of observed filling events can also be requested using this interface and used for e.g. plausibility controls.
By only using the RS232 interface also present in CFO color sensors a local information processing solution would be needed for piping sensor data into a central process database. Provisioning this data though the network interface removes this need for additional hardware as collection of sensor data can now be implemented centrally using existing IT resources.
Detecting adhesive strips on diapers
Marion Donovan has been granted a patent for the invention of disposable diapers in 1951. 1946 she was sewing her first diaper shorts from shower curtains. They were meant to be worn over cloth diapers. Three years later she brought the first disposable diapers, named Boater, to market. But at this time neither she nor her various copycats were economically successful. That only changed as Proctor & Gamble released their version, called Pampers, in 1961. Five years earlier Victor Mills, head of research at the corporation, developed that version. Since then disposable diapers developed into a real high tech product. Today disposable diapers are an incredibly popular product. Given the about 10 million toddlers just in the United States have to get new diapers about 3 to 5 times a day, there is a daily (!) demand of up to 40 million diapers. This is a yearly demand of about 15 billion diapers just in the United States!
To meet this demand, diaper producers usually employ multiple production lines. Along a line of over 50m a diaper production machine creates over 100 diapers per minute.
A modern disposable diaper has, beneath absorbent core, internal fleece, external material, cuffs and leakage barrier, one critical feature: adhesive strips. These fasteners are in use since 1995 and consist of one part with small loops and one part with flexible barbs.
Different sizes as batches of diapers are coded with different adhesive strips. This is implemented through different motives printed in various base colors. A running production process demands 100% reliable controlling of the correct strips are used in a batch. End final inspection before packaging has to ensure that diapers of the correct size get into the packaging.
The adhesive strips glued onto the diapers have colorful patterns, which heightens the demands on optical precision even more than the high processing speeds. The base material has to be detected reliably and in a second step the border of the strip has to be detected and evaluated.
The CFO100 color sensor, boasting a sampling rate of 10kHz and a color precision of delta E < 0.8, can reliably detect the adhesive strips. The color impression of a particular strip gets averaged and the result is compared to a pretrained color impression. At the same time correct positioning of the adhesive strip is evaluated at full production speeds. Because of its high sampling rate CFO100 is a good fit for the task at hand.
Tasks
- Inspection of presence of a strip
- Evaluation of correct assignment of diaper to packaging
- Sorting of the end product
Implementation
The CFO100 color sensor gets integrated in-line into the production chain, shortly before packaging. Using a fiber optical cable and suiting optics an optimal measung spot diameter is created. The color sensor illuminates precisely the expected position of the adhesive strip. If the current measurement equals the pretrained color impression, the corresponding signal is sent to the switching outputs.
Using the integrated HTTP API processing changes (like different diaper types, new colors or changes in timing) can be centrally organized and sent to all sensors across production lines.
Have we sparked your interest?
CFO color sensors are distributed exclusively by Micro-Epsilon. Please feel free to contact at:
+49 8542 / 168 - 0
info@micro-epsilon.de